latest news
Why do I need to recertify my fall protection systems?
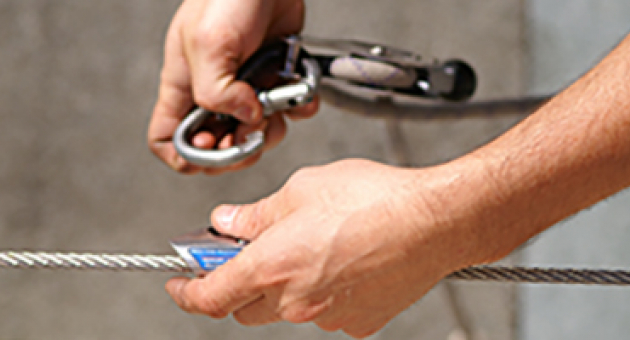
We all know the importance of getting our cars regularly inspected and maintained. Not getting your car serviced and MOT’d can lead to breakdowns, or even legal trouble for failing to meet your responsibilities as an owner.
So, if this is true of our cars, which we trust our lives to every day, why would the same not be true of our fall protection systems?
From guardrails to lifelines and anchor points, fall protection systems are a vital part of keeping workers safe when they access a roof to carry out maintenance or other types of roof activity, and it is important to keep them in top condition.
Who is responsible?
If you are the owner of a building, or an occupier with responsibility for the building, then you are legally required to ensure that your work at height safety systems are safe for use by employing a competent third party to inspect and recertify them on a regular basis.
If you fail or refuse to ensure these responsibilities are met, and there is a safety failure, you, the building owner or managing director of the company could be held responsible for any injuries or deaths that occur. This can mean a heavy fine, or even a prison sentence depending on the severity of the incident.
What is worse, falls from height can change or even end lives in an instant, which is something that nobody wants on their conscience.
Is recertification really that important?
Yes. All fall protection systems can fail, whether through lack of maintenance, harsh environments, or rusted components. Initial poor installation through third parties can also mean that systems fail much quicker.
Contractors who visit site to carry out other work may modify these systems as part of their work, causing failures without even realising it. Systems can also be accidentally deployed without anyone noticing, making them useless when needed.
Personal fall protection systems, such as lifelines, are more prone to failure than collective systems such as guardrails as they have more moving parts, but collective systems can still degrade over the years and become useless.
To ensure you comply with current standards, such as EN 365, ENBS 7883, EN 795 and the Working at Height Regulations, you should have your fall protection equipment inspected and recertified every twelve months, as well as carrying out regular pre-use checks every time the system is used.
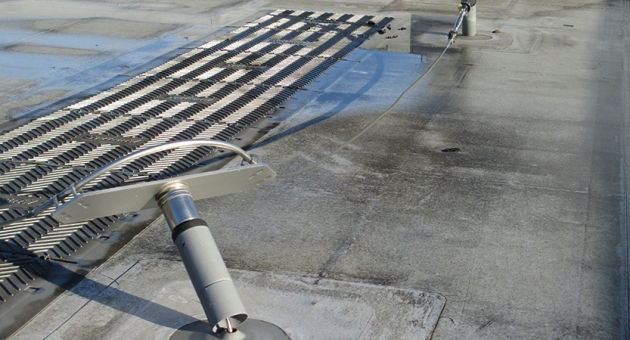
Who can recertify my equipment?
You should select an independent and competent recertification company to fully inspect your equipment.
To ensure competency, you should check whether they are a member of a recognised industry group or association, and that they have the relevant health and safety accreditation, such as Safecontractor. These groups and accreditations require members to be regularly vetted and trained, providing peace of mind.
The company you hire should also be able to demonstrate their competency by providing you with the correct training certificates.
Roof Edge carries out hundreds of recertifications a year on sites across Scotland. We inspect and recertify all aspects of working at height from collective to personal protection and any associated PPE.
Upon inspection, we will provide you with an industry standard certification, or a schedule of improvement works to ensure you meet the expected level of safety.
For more information about our recertification service, call us on 0141 949 1014, or use our online contact form.
Related posts: